Understanding How Burner Management Systems Work
- gradymoore7
- Oct 2, 2024
- 22 min read
Introduction to Burner Management Systems (BMS)
Burner Management Systems (BMS) are critical components in industrial operations, designed to monitor the startup, operation, and shutdown of burner units. These systems are essential for ensuring the safe and productive operation of burners, which are commonly used in industries such as oil and gas, power generation, and manufacturing. By providing automated control over burner functions, a BMS minimizes the risk of accidents, reduces operational downtime, and enhances overall process efficiency. The importance of implementing a robust burner management system cannot be overstated, as it plays a vital role in maintaining safety standards and optimizing industrial performance.

What Does a Burner Management System Do?
Burner Management Systems (BMS) are designed to ensure the safe operation of industrial burner units. By automating and controlling critical aspects of burner functions, a BMS helps maintain compliance with safety regulations, enhancing overall system reliability.
Safety Functions
A key role of a burner management system is to ensure the safe startup, operation, and shutdown of burners. Safety is paramount in industrial environments, and a BMS provides multiple layers of protection to prevent accidents. Throughout the operation, the BMS continuously monitors key parameters, such as temperature, pressure, and flame status, ensuring that all conditions remain within safe limits.
One of the critical features of a BMS is its use of automated safety interlocks. These interlocks are programmed to immediately shut down the burner if any unsafe condition is detected, such as loss of flame or excess pressure. This immediate response capability minimizes the risk of incidents that could lead to equipment damage or safety hazards. In addition to automated controls, a BMS also includes manual override functions, allowing operators to intervene directly if necessary, providing an additional layer of safety in emergency situations.
Key Components of a Burner Management System
Burner management systems (BMS) are composed of several key components that work together to ensure the proper operation of burner units. Each component is fundamental in monitoring — and when necessary, controlling — the burner's performance. Below, we discuss the essential elements of a BMS, including sensors and detectors, control logic and software, actuators and valves, and the human-machine interface (HMI).
Sensors and Detectors
Sensors and detectors are critical to the functioning of burner management systems, providing real-time data that informs safety and control decisions. Common types of sensors used in BMS include flame detectors, temperature sensors, and pressure transducers. Flame detectors monitor the presence and quality of the burner flame, ensuring that it remains stable and within safe parameters. Temperature sensors track the heat levels within the burner and the surrounding environment, helping to prevent overheating and maintain optimal combustion conditions. Pressure sensors monitor gas and air pressures, ensuring that they are within safe operating limits.
These sensors and detectors are indispensable elements of safeguarding burner operations. By continuously monitoring key parameters, they enable the BMS to quickly detect any deviations from normal operating conditions. This early detection allows the system to take immediate corrective action, such as adjusting fuel and air flows or shutting down the burner, to prevent unsafe situations and maintain effective operation.
Control Logic and Software
The control logic and software are the brains of a burner management system. They utilize complex algorithms to analyze data from sensors and make real-time decisions about burner operation. These control algorithms are designed to ensure safety. The software manages the sequence of operations, from the initial purge sequence to shutdown, and responds to changes in burner status or external conditions.
Control logic also plays a role in managing safety interlocks and override procedures, ensuring that the burner operates only when all safety conditions are met. This systematic approach to control not only enhances safety but also improves the reliability and consistency of burner performance. By automating these processes, the BMS reduces the likelihood of human error and allows for precise, consistent control over burner functions.
Actuators and Valves
Actuators and valves are essential components of a burner management system, responsible for enabling the burner’s fuel supply and air flow. Actuators receive commands from the BMS software to allow the flow of gas or liquid fuel and combustible air to the burner.
Valves also play a critical role in safety, acting as barriers to prevent fuel from flowing when unsafe conditions are detected. For instance, a BMS can close fuel valves immediately in response to a detected flameout or pressure anomaly, preventing the release of unburned fuel and mitigating the risk of fire or explosion. Through the coordinated action of actuators and valves, burner management systems, in conjunction with combustion control systems (CCS), can maintain optimal operating conditions while ensuring the highest levels of safety.
Human-Machine Interface (HMI)
The Human-Machine Interface (HMI) is a vital component of burner management systems, providing operators with a user-friendly platform to interact with the BMS. Through the HMI, operators can monitor burner status, view real-time data from sensors, and access diagnostic information. HMIs often feature graphical displays that make it easy to visualize burner performance, safety status, and system alerts.
In addition to monitoring, the HMI allows operators to manually control burner operations, adjust setpoints, and respond to alarms. This capability is essential for troubleshooting and maintenance, giving operators the tools they need to ensure continuous and safe burner operation. The HMI also logs data for reporting and analysis, helping operators optimize burner performance over time. By providing a clear and intuitive interface, the HMI enhances the effectiveness of the burner management system and supports safe and optimized operation.
How Do Burner Management Systems Integrate with Combustion Control Systems (CCS)?
A Combustion Control System (CCS) is responsible for regulating the precise mixture of fuel and air required for optimal combustion in industrial burners. The CCS monitors and adjusts fuel flow and airflow to ensure efficient combustion, reduce emissions, and maximize fuel efficiency. It works closely with the Burner Management System (BMS), which primarily oversees the safety aspects of burner operation, including purge, startup, shutdown, and emergency conditions. Together, the BMS and CCS form an integrated control and safety system, with the BMS ensuring safe operation while the CCS maintains efficiency of the burner unit. This tight integration ensures that both safety and efficiency are prioritized throughout the entire combustion process.

What Are the Operational Modes of a Burner Management System?
Burner management systems (BMS) are integral to the safe operation of industrial burners. By understanding how burner management and combustion control systems operate, facilities can better manage their combustion processes, optimize performance, and maintain high safety standards. This section provides insights into the operational modes of a BMS, the typical sequence of burner operation, and common troubleshooting and diagnostic practices.
Automated vs. Manual Operation
Burner management systems can operate in both automated and supervised manual modes, each offering distinct advantages depending on the situation. In automated mode, the BMS uses pre-programmed logic to monitor the entire operation of the burner, from the purge sequence to shutdown. This mode is highly efficient, as it reduces the need for human intervention, minimizes the risk of error, and ensures consistent adherence to safety protocols. Automated operation is ideal for normal, routine burner activities where conditions are stable, and the risk of unexpected incidents is low.
Conversely, manual mode — which is more accurately described as supervised manual — allows operators to directly control burner functions, bypassing some automated processes when needed. This mode is essential when performing maintenance and troubleshooting tasks. Manual operation is preferable in scenarios where customized control is necessary, or when operators need to respond to specific conditions that may not be adequately addressed by automated systems. It provides the flexibility to handle unexpected situations and ensure safety when automated systems may not cover every possible scenario.
What Are Typical Operation Sequences of Burner Management Systems?
A typical burner management system follows a structured sequence of operations to maintain safety and efficiency.
Startup Sequence - Purging
Prior to the actual light-off, operators must complete the purge sequence. This portion of the operation sequence is designed to remove any unburned hydrocarbons, combustible gases, or other volatile substances that may remain inside the firebox since the last shutdown. This step is crucial for ensuring that the firebox is clear of potentially explosive mixtures that could ignite unexpectedly if exposed to an ignition source.
Completing the purge sequence before introducing fuel into the system is essential for preventing flashbacks and explosions. By ensuring that the firebox is free of unburned hydrocarbons and residual gases, the BMS helps maintain a safe environment for ignition, thereby protecting equipment and personnel from the hazards associated with unexpected combustion. The effectiveness of the purge sequence is typically verified by monitoring airflow and pressure, ensuring that the system is ready to safely proceed to the light-off.
Startup Sequence - Light-off
Once the purge sequence is complete, the system then initiates the light-off — during which, the pilot and the main burner(s) are ignited. Once the burner’s flame is stabilized, the BMS will release control of the equipment to the combustion control system (CCS).
Normal Operation
During the normal operation, the combustion control system (CCS) retains primary control of the equipment while the burner management system monitors the safety aspect of the burner operation in the background. In the event that the BMS detects the equipment is going beyond its safe operating limit (ex: loss of flame, too much air or fuel flow, too much pressure, etc.), the BMS will override the CCS, taking back control of the equipment to return the process to a safe state by tripping the shutoff valves for the fuel flow.
Shutdown Sequence
There are two types of shutdown sequences, normal shutdown and emergency shutdown. During a normal shutdown sequence, the operator gradually reduces fuel and air supply via the CCS, extinguishing the flame in a controlled manner while the BMS continues monitoring for unsafe conditions.
During an emergency shutdown, the operator presses an emergency shut down (ESD) button, triggering the BMS to immediately cut off fuel supply going to the burners, bringing the burners unit to a safe state.
Troubleshooting Common Issues of Burner Management Systems

Effective troubleshooting and diagnostics are crucial when dealing with burner management systems, helping to identify and resolve issues that can affect performance and safety. Some of the more common issues found in BMSs include sensor malfunctions, ignition failures, and unexpected shutdowns. These issues can arise from a range of factors, such as equipment wear and tear, environmental conditions, or deviations in process parameters.
A BMS is equipped with diagnostic tools that continuously monitor system performance and alert operators to potential problems. For example, if a sensor detects a deviation from expected temperature ranges, the system generates an alarm, prompting operators to investigate. Advanced diagnostics can provide detailed information about the issue, such as the specific sensor or component involved, the nature of the deviation, and recommended corrective actions.
Troubleshooting typically involves a systematic approach, starting with reviewing alarm logs and diagnostic reports to identify the root cause of the problem. Operators may then perform manual checks or use diagnostic software to test system components. Once the issue is identified, corrective actions may include adjusting control settings, replacing faulty sensors, or performing maintenance on valves and actuators. By promptly addressing issues, a BMS helps maintain safe and reliable burner(s) operation, minimizing downtime and ensuring compliance with safety standards.
What is the NFPA Code/Standard for Burner Management Systems?
Compliance with relevant safety codes and standards is essential to maintain optimal operation and protect both personnel and equipment. The National Fire Protection Association (NFPA) provides specific guidelines for fired equipment through its NFPA 85 code, which addresses safety protocols for boiler and combustion systems as well as NFPA 86 standard, which covers ovens and furnaces and NFPA 87 standard for thermal and process fluid heaters.
What is the NFPA 85 Code?
The National Fire Protection Association (NFPA) is a global organization dedicated to eliminating fire-related hazards through the development of safety codes and standards. NFPA code and standards are widely recognized and adopted across industries, providing comprehensive guidelines to ensure safety in various operational settings. One of the key NFPA codes and standards relevant to burner management systems is the NFPA 85 code, known as the Boiler and Combustion Systems Hazards Code.
The NFPA 85 code sets forth requirements for the design, installation, operation, and maintenance of combustion systems used in boilers, including those managed by burner management systems. The code is applicable to a wide range of industries, such as power generation, chemical processing, and oil and gas, where the safe operation of boilers is paramount. By adhering to the NFPA 85 code, organizations can ensure that their BMS meet stringent safety standards, reducing the risk of fire, explosion, and operational disruptions.
What Are the NFPA Codes & Standards Burner Management System Compliance Requirements?
NFPA codes and standards outline several key safety standards and compliance requirements that burner management systems must meet to ensure safe operation. These requirements focus on critical aspects of BMS design and functionality, including, but not limited to:
Safety Interlocks
NFPA codes and standards mandate the use of safety interlocks to prevent unsafe conditions during burner startup, operation, and shutdown. These interlocks ensure that all safety conditions are met before the burner can be ignited, and they automatically shut down the burner if any unsafe conditions are detected during normal operations.
Redundancy and Reliability
NFPA codes and standards require redundancy in critical components of the BMS, such as sensors and control systems, to enhance reliability and minimize the risk of failure. Redundant systems ensure that backup components can take over in case of primary component failure, maintaining safe and continuous operation.
Burner Management System Application Logic
NFPA codes and standards specify the use of structured control logic to manage burner operations. This includes clear definitions of startup and shutdown sequences, as well as protocols for responding to alarms and deviations. The control logic must be designed to prevent unsafe conditions and ensure that the burner operates within safe limits.
Testing and Maintenance
Regular testing and maintenance of burner management systems is required to ensure that all components function correctly. NFPA codes and standards provide guidelines for the frequency and scope of testing, as well as procedures for maintaining and repairing BMS components. It is typically advised to inspect a BMS at least once a year, though more frequent inspections might be necessary based on operating conditions and compliance with regulatory requirements.
Importance of Compliance
Compliance with NFPA codes and standards is crucial for both regulatory and operational reasons. From a regulatory standpoint, adherence to NFPA codes/standards is often a legal requirement, with regulatory bodies and insurance companies frequently mandating compliance to ensure safe and responsible operations. Failure to comply can result in fines, legal liabilities, and increased insurance premiums, all of which can significantly impact a business.
Operationally, compliance with NFPA codes/standards enhances the safety and reliability of burner management systems, protecting personnel and equipment from fire and explosion hazards. By following the guidelines set forth in the code, organizations can reduce the likelihood of accidents, while minimizing downtime. Moreover, adherence to NFPA codes/standards demonstrates your facility’s commitment to safety and best practices, enhancing the reputation of the organization and building trust with stakeholders.
Overall, understanding and complying with the NFPA codes and standards for burner management systems is necessary for maintaining high safety standards, meeting regulatory requirements, and ensuring reliable burner operation.
What are the Benefits of Implementing a Burner Management System?
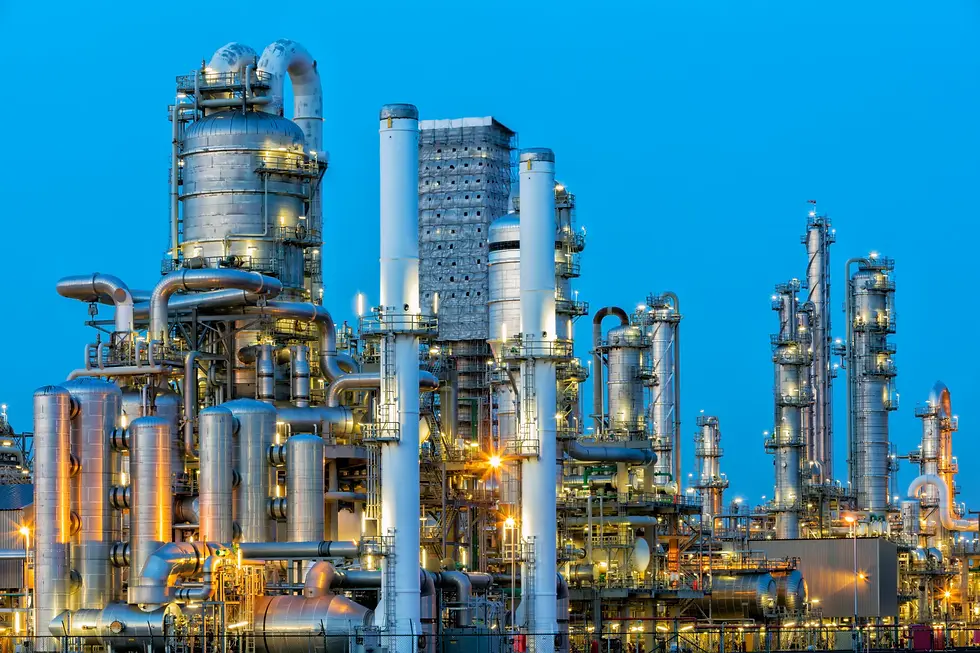
Implementing burner management systems (BMS) offers numerous advantages for industrial operations, from enhanced safety and regulatory compliance to potential cost savings. These systems play a central role in managing burner operations, ensuring that they run safely while adhering to industry standards. Below, we discuss a few of the benefits of integrating a BMS into your facility.
Enhanced Safety
One of the primary benefits of a burner management system is its ability to significantly reduce the risk of accidents. By automating the control of burner operations and continuously monitoring critical parameters, a BMS ensures that burners operate within safe limits. This automation minimizes the chance of human error, which is often a leading cause of accidents in industrial settings. Safety interlocks and sensors detect any deviations from normal operating conditions, triggering immediate corrective actions or shutdowns to prevent unsafe situations.
The comprehensive safety features of a BMS, such as flame detection, pressure monitoring, and temperature control, help protect personnel, equipment, and facilities from potential hazards. By preventing incidents like flameouts, gas leaks, and overheating, a BMS contributes to a safer work environment, reducing the likelihood of injuries and equipment damage. This enhanced safety is critical in industries where the consequences of accidents can be severe, such as oil and gas, chemical processing, and power generation.
Regulatory Compliance
Adhering to industry standards and regulations is essential for any industrial operation, and burner management systems play a major role in ensuring compliance. Many industries are subject to stringent safety and environmental regulations, such as those outlined by NFPA codes/standards and other relevant codes. As explained above, a properly implemented BMS helps facilities meet these regulatory requirements by ensuring that burners operate as intended, with appropriate controls in place.
Compliance with regulations not only helps avoid legal penalties and fines but also enhances the credibility and reputation of your organization. By demonstrating a commitment to following industry standards, companies can build trust with regulatory bodies, customers, and stakeholders. This commitment to compliance can often play a role in maintaining certain operational licenses and securing insurance coverage, both of which are essential for a business.
Potential Cost Savings
The long-term financial benefits of installing and maintaining a burner management system can prove to be substantial. By enhancing safety and reducing the risk of accidents, a BMS helps avoid costly incidents, equipment damage, and potential legal liabilities. The investment in a BMS can also lead to lower insurance premiums, as insurers often recognize the reduced risk associated with automated safety systems.
A burner management system can also result in cost savings by minimizing downtime and lost production due to equipment damage as a result of operation beyond acceptable parameters. By improving process control and extending the lifespan of equipment, a BMS can contribute to lower operating costs and increased profitability. Over time, the initial investment in a burner management system can pay for itself through these ongoing savings, making it a wise choice for any industrial operation focused on safety, efficiency, and cost-effectiveness.
The benefits of implementing a burner management system are multifaceted, offering enhanced safety, regulatory compliance, and potential cost savings. These advantages make BMSs an essential component of modern industrial processes, ensuring that burners operate safely and in compliance with industry standards.
Types of Burner Management Systems
Burner management systems (BMS) come in various configurations, each designed to meet specific operational needs and requirements. Choosing the right type of BMS depends on several factors, including the number of burners, whether the system is being retrofitted or newly installed, and the level of customization needed. Understanding these options can help organizations select the most effective BMS for their applications.
Single Burner vs. Multi-Burner BMS
One of the primary distinctions in burner management systems is between single burner and multi-burner configurations. Single burner systems, as the name suggests, are designed to manage a single burner unit. These systems are typically used in applications where one burner provides all the necessary heat or energy, such as in small boilers or individual process heaters. Single burner BMSs are usually simpler in design, focusing on the control and safety requirements of a single combustion unit. They are often easier to install, operate, and maintain, making them a cost-effective choice for smaller operations.
In contrast, multi-burner systems are — as you might imagine — used to manage multiple burners simultaneously, often in larger industrial applications such as power plants, large boilers, or chemical processing facilities. A multi-burner BMS must coordinate the operation of several burners, ensuring that each unit operates safely while maintaining overall system stability. These systems require more sophisticated control logic and safety interlocks to handle the complexities of managing multiple burners.
Single Fuel vs. Multi-Fuel Fired Burners BMS
Most industrial burners are designed to operate on a single type of fuel, such as natural gas, diesel oil, or propane. Single-fuel burners offer a streamlined and simplified approach to burner management, as the BMS is designed to monitor one specific type of fuel. This can make operation, maintenance, and regulatory compliance more straightforward. However, in certain situations, a company may opt to use multi-fuel fired burners, which can operate on more than one fuel type.
The decision to implement multi-fuel burners is often driven by economic considerations, such as fluctuations in fuel prices. For example, a facility may choose a burner system that can switch between natural gas and diesel oil depending on which fuel is more cost-effective at any given time. This flexibility can provide significant operational savings, particularly in industries where fuel costs represent a substantial portion of overall operating expenses.
When choosing between single-fuel and multi-fuel burners, it is important to consider how the decision will impact your burner management system. A BMS for a multi-fuel system must be more advanced, capable of accommodating each fuel type used. Ensuring that the BMS can seamlessly transition between fuel types without compromising safety is essential for optimizing operations in multi-fuel burner systems. Therefore, facilities should carefully evaluate their fuel needs and corresponding safety hazards when choosing a BMS that aligns with both current operational and safety requirements and future flexibility.
BMS Retrofit vs. New Installation
When implementing burner management systems, facilities can choose between retrofitting existing equipment or installing a completely new system. Retrofit solutions involve upgrading or enhancing the existing BMS equipment to meet current safety standards. Retrofitting can be a cost-effective option for facilities with older equipment that still has a significant remaining lifespan. It allows organizations to enhance safety without the need for extensive capital investment in new equipment. Retrofit solutions can also be customized to integrate with existing systems, minimizing downtime during installation.
On the other hand, new burner management system installations are ideal for projects involving new construction or complete system overhauls. Installing a new BMS allows for the latest technology and standards to be implemented from the start, ensuring optimal safety and efficiency. New installations provide the opportunity to design a system that precisely meets the specific requirements of the application, with the flexibility to incorporate the latest advancements in BMS technology. While new installations may require a larger initial investment, they can offer long-term benefits in terms of reliability, performance, and compliance with the latest regulatory standards.
Custom vs. Off-the-Shelf Burner Management Systems
Burner management systems can be either customized or off-the-shelf solutions — often referred to as pre-programmed and configurable systems, respectively —, each offering distinct advantages. Custom BMS solutions are tailored to meet the specific needs of a particular application or facility. Customization allows for the integration of unique features, specific control strategies, and specialized safety requirements. A custom BMS is ideal for complex operations or industries with stringent safety regulations, where standard solutions may not fully address all operational needs. However, custom systems may involve higher development costs and longer implementation times due to the need for specialized design and engineering.
In contrast, off-the-shelf (OTS) BMS solutions are pre-designed and pre-programmable systems that offer standardized features and functionalities suitable for a wide range of applications. These systems are typically quicker to deploy and less expensive than custom solutions, making them an attractive option for facilities with more straightforward requirements. Off-the-shelf burner management systems provide reliable performance and compliance with industry standards, making them suitable for many common industrial applications. The main drawback is that they may offer less flexibility in terms of customization and may not fully meet the unique needs of more specialized operations.
The choice between a system that is single and multi-burner, single or multi-fuel, retrofit versus new installation, and custom versus off-the-shelf solutions depends on various factors, including the size and complexity of the operation, budget considerations, and specific safety and performance requirements. Understanding these options helps organizations select the most appropriate burner management system to ensure optimal operation.
How to Choose the Right Burner Management System
Selecting the appropriate burner management system is paramount in ensuring the safe and reliable operation of your burners unit. With multiple options available, it's important to consider multiple factors to make an informed decision.
Factors to Consider
When selecting a burner management system, several factors must be considered to ensure that the system meets the specific requirements of your application. The type of application is a primary consideration — whether you are managing a single burner vs. multi-burner and single fuel vs. multiple fuel setup, the BMS must be designed to handle the complexity and scale of your operations. Additionally, the type of fuel being used, whether natural gas, oil, or another fuel, will influence the design and configuration of the BMS. Each fuel type has unique characteristics that must be accounted for to ensure the desired levels of combustion.
Environmental conditions are another factor to keep in mind. The operating environment, including temperature, humidity, and potential exposure to corrosive elements, can impact the performance and durability of a BMS. Systems designed for harsh or hazardous environments may require additional protective features, such as specialized enclosures or components rated for extreme conditions. Understanding these factors will help you select a BMS that is both effective and durable in your specific operating environment.
Cost Considerations
Budgeting is an essential aspect of choosing a burner management system. The costs associated with a BMS extend beyond the initial purchase and installation; ongoing maintenance and operational expenses should also be considered. It’s important to evaluate the total cost of ownership, including the potential need for spare parts, routine maintenance, testing, and periodic upgrades. While it may be tempting to opt for a lower-cost solution, it is important to balance initial costs with long-term reliability and efficiency. A higher upfront investment in a quality BMS can lead to significant savings over time by reducing downtime and minimizing the risk of costly accidents.
Additionally, consider the costs associated with training personnel to operate and maintain the system. Some BMS options may require specialized knowledge or certifications, which could influence both the initial training expenses and the ease of finding qualified operators and maintenance staff.
Future Proofing
As industrial processes and technologies continue to evolve, it’s important to choose a burner management system that can adapt to future needs. Future proofing your BMS involves selecting a system that is not only compatible with current technologies but also scalable and flexible enough to incorporate future advancements. Look for systems that offer modular designs, allowing for easy upgrades or expansions as your operational requirements change.
Integration capabilities are another important consideration. A BMS that can easily interface with other systems, such as combustion control, distributed control systems (DCS), or safety instrumented systems (SIS), will provide greater flexibility and functionality in the long term. Additionally, consider whether the BMS manufacturer provides ongoing support and updates to keep your system in line with the latest technological developments and regulatory requirements.
By thoroughly evaluating these aspects, you can select a BMS that not only meets your current needs but also positions your operations for long-term success and safety. Many facilities choose to work with an experienced BMS solutions provider like aeSolutions once the decision to add or upgrade a BMS has been made. Bringing in a trusted engineering firm for your BMS needs, can make a significant impact on how quickly and efficiently your burner management system is designed and implemented.
Installation and Maintenance of Burner Management Systems

Proper installation and maintenance are integral for the effective operation of burner management systems. Ensuring that these systems are installed correctly and maintained regularly helps maximize their efficiency and reliability. Below, we take a look at the typical installation process, the importance of regular maintenance, and considerations for upgrades and modernization.
Burner Management System Installation Process
The typical installation of a burner management system involves several steps to ensure that the system is properly integrated into the existing infrastructure. The process usually begins with a thorough site assessment, during which the specific requirements and conditions of the installation environment are evaluated. This assessment helps determine the appropriate configuration of the BMS, including the placement of sensors, control units, and other components.
Once the assessment is complete, the next step involves designing the system layout, ensuring that all components are positioned for optimal performance and safety. Following the design phase, installation technicians proceed with wiring and connecting the BMS components, including sensors, actuators, and control panels. Testing is a vital part of the installation process, involving rigorous checks to verify that all components are functioning correctly, and that the system responds appropriately to various operating conditions.
To minimize downtime during installation, facility managers should plan and coordinate with facility operators. Scheduling the installation during planned maintenance periods or low-production times can help reduce the impact on overall operations. Additionally, using pre-configured or modular BMS components can streamline the installation process and reduce the time required for setup and commissioning.
Regular Maintenance and Inspections
Routine maintenance and periodic inspections and testing are essential to ensure the longevity and reliability of burner management systems. Regular maintenance helps identify and address potential issues before they lead to system failures or unsafe conditions. Maintenance tasks typically include checking the functionality of sensors and detectors, inspecting wiring and connections for signs of wear or damage, and testing safety interlocks and control logic.
Periodic inspections and testing are also important for verifying that the BMS remains in compliance with relevant safety standards and regulations. These inspections and testing may involve reviewing system performance data, conducting safety drills, testing safety interlocks, and updating system software or firmware. Regularly calibrating sensors and testing alarm systems ensures that the BMS continues to operate accurately and effectively, maintaining the highest levels of safety, reliability, and availability.
Establishing a preventive maintenance schedule is considered a best practice for managing the upkeep of a BMS. By performing routine checks and maintenance tasks at defined intervals, organizations can reduce the likelihood of unexpected downtime and extend the lifespan of their burner management systems.
Upgrades and Modernization
Upgrading or modernizing an existing burner management system is sometimes necessary to meet new safety standards, improve performance, or incorporate advanced features. Advancements in technology may also prompt the need for system upgrades. Upgrading a BMS can enhance its functionality, improve safety features, and increase reliability.
The decision to upgrade should be based on a comprehensive evaluation of the current system's performance, age, and compatibility with new technologies. When planning an upgrade, it is important to consider factors such as the compatibility of new components with existing equipment, the potential impact on operations, and the long-term benefits of the upgrade.
Modernization projects often involve integrating advanced control algorithms for diagnostics, upgrading sensors to more accurate or reliable/smart models, and enhancing the human-machine interface (HMI) for better operator interaction. Additionally, upgrading software to the latest version can improve system functionality and ensure that the BMS is equipped to handle emerging operational challenges.
By following best practices during installation, performing regular maintenance and inspections, and considering timely upgrades, organizations can maximize the performance and reliability of their BMS, helping to ensure compliance with industry standards and safeguarding their operations.
The Takeaway | Burner Management Systems
Burner management systems are a core component to the safe operation of industrial burners, playing an essential role in numerous industries such as oil and gas, power generation, and manufacturing. These systems provide automated control over the critical functions of burner operations, from startup through shutdown, ensuring compliance with stringent safety standards. Understanding the components and functionality of BMS, including sensors, control logic, and human-machine interfaces, is key to leveraging their full potential. Adhering to NFPA codes and standards requirements and integrating robust maintenance and upgrade practices can also significantly enhance the safety, reliability, and longevity of these systems. By carefully selecting, installing, and maintaining a burner management system, facilities can not only meet regulatory demands but also achieve long-term cost savings, operational efficiency, and a safer working environment. As industrial processes evolve, the importance of a well-implemented BMS becomes more apparent, ensuring that industrial burner operations remain at the forefront of safety and reliability standards.
Burner Management Systems Frequently Asked Questions (FAQ)
What are the Common Safety Risks Addressed by a BMS?
Burner management systems are designed to mitigate several safety risks associated with the operation of industrial burners. These risks include flame failure, which can lead to the accumulation of unburned fuel, posing a significant explosion hazard. A BMS addresses this risk by using flame detectors and safety interlocks that immediately shut down the burner if a flame is not detected.
Another safety risk is overheating, which can cause damage to equipment and create unsafe conditions. Temperature sensors within the BMS continuously monitor burner temperatures, ensuring they remain within safe limits. Furthermore, a BMS can help prevent gas leaks and pressure anomalies by monitoring and controlling fuel and air supply lines. By providing automated shutdowns and alerts, a BMS helps prevent potentially dangerous situations, protecting personnel and equipment from harm.
How Long Does It Take to Install a BMS?
The installation time for a burner management system can vary depending on several factors, including the complexity of the system, the size of the facility, and the specific requirements of the installation. Typically, the actual installation process of a standard BMS can take anywhere from a few days to several weeks. The process involves conducting a site assessment, designing the system including layout, control panels, configuring/programming, installing hardware components, wiring and connecting sensors and control units, and performing extensive testing.
For more complex installations, such as those involving multi-burner systems or facilities with unique operational requirements, the installation process may take longer. Proper planning and coordination with facility operations can help minimize installation time and reduce the impact on production schedules.
What is the Expected Lifespan of a Burner Management System?
The expected lifespan of a burner management system largely depends on the quality of the components used, the operating environment, and the maintenance practices in place. On average, a well-maintained BMS can last between 10 to 20 years. Regular maintenance, including inspections, calibration of sensors, and software updates, plays a significant role in extending the lifespan of the system.
Environmental factors, such as exposure to extreme temperatures, humidity, or corrosive substances, can also impact the durability of a BMS. Choosing a system designed to withstand specific environmental conditions and adhering to a preventive maintenance schedule can help maximize the lifespan of the system.
How Often Should a BMS be Inspected or Maintained?
Routine inspections and maintenance are critical to ensuring the reliable operation of a burner management system. It is generally recommended that a BMS be inspected at least annually, although more frequent inspections may be required depending on the operating conditions and regulatory requirements. During these inspections, technicians should check the functionality of sensors, safety interlocks, control logic, and alarm systems.
In addition to annual inspections and testing, certain maintenance tasks, such as sensor calibration and visual checks of BMS equipment, should be performed more frequently. A quarterly maintenance schedule is often advised for high-use systems or those operating in harsh environments. By adhering to a regular maintenance schedule, organizations can ensure that their BMS continues to operate effectively, maintaining safety and reliability standards.
Comments