What is a Dust Hazard Analysis (DHA)? | Pt. 5
- beckykramer7
- Jun 5, 2023
- 5 min read
Updated: Aug 23, 2024
Understanding a Dust Hazard Analysis (DHA)
Following on from the first four aeSolutions blogs on the subject of combustible dust concerns, this blog provides another deep dive into the topic. We previously addressed the basic concerns around combustible dusts, many of the standards that address dust hazard guidance, and the properties and testing for combustible dusts; potential ignition sources; and potential safeguards. This article will build on those topics to pull it all together and review a commonly used dust hazard analysis (DHA) method.
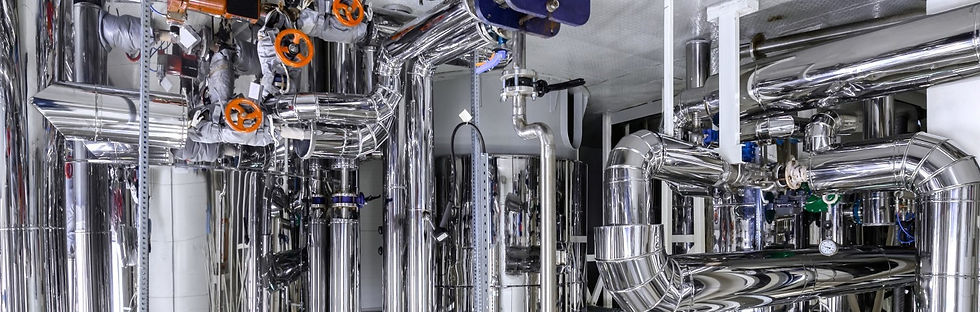
The Challenges | Dust Hazard Analysis (DHA)
A Dust Hazard Analysis or DHA is an important method to assess the risk posed by ignition of combustible dusts. Companies handling highly hazardous chemicals (HHC) routinely conduct process hazard analyses (PHAs), but it is not common to encounter PHAs that thoroughly review combustible dust hazards or company internal standards that address combustible dust hazards. Many companies’ PHAs do not address combustible dust hazards in an organized manner or in a manner that complies with industry guidance on dust hazard analyses (DHA), if the dust hazards are reviewed at all.
Why Would You Conduct a Dust Hazard Analysis For a Combustible Dust Process?
There are several reasons, and the most obvious is to protect people, the environment, assets, and reputation from dust explosions and fires. Other reasons for a Dust Hazard Analysis (DHA) include:
The OSHA general duty clause requires that, in addition to compliance with hazard-specific standards, all employers provide a work environment "…free from recognized hazards that are causing or are likely to cause death or serious physical harm." A company may identify the need for a Dust Hazard Analysis on an existing combustible dust process internally due to this requirement.
A dust explosion incident involving a dust with identical or similar properties to that in an existing process may occur.
An industrial hygiene review of process dust or particulates may identify combustibility concerns.
A PHA team may identify the need for a deeper dive into dust risks.
A codes and standards review may identify NFPA 652 (Standard on the Fundamentals of Combustible Dust) as a needful standard for compliance. NFPA 652 is considered to be a Recognized And Generally Accepted Good Engineering Practice (RAGAGEP).
An insurance company providing coverage for the facility may request it.
How to Conduct a Risk-Based Dust Hazard Analysis
A Dust Hazard Analysis is a focused method to improve facility safety by identifying combustible dust hazards and necessary safeguards associated with a process. There are variations across companies on how DHAs are conducted, similar to the many variations on PHAs that can be found in industry, but there are two basic approaches: a traditional approach based on an engineering analysis and standards compliance; and a risk based approach. Most companies opt for a risk-based approach and those basic steps are described here:
Identify the relevant properties of a combustible dust (as described in part 2 of this series).
Form a suitable team to perform the Dust Hazard Analysis, including a qualified facilitator.
Determine which internal and industry standards apply to the Dust Hazard Analysis and educate team members on those standards. (There is a partial list of applicable industry standards in part 1 of this series.)
Assemble or develop the process safety information that the Dust Hazard Analysis team will need, including equipment ratings, electrical area classification designations, dust data, safe operating ranges, operating procedures, housekeeping protocols, and current maintenance regimes, among other data. If there are existing mitigating safeguards (as described in part 4 of our Dust Hazard Analysis series), data on those systems should also be readily available.
With guidance from a qualified facilitator, the team develops the credible dust cloud and dust layer scenarios internal and external to the equipment.
The team identifies the credible internal and external ignition sources for each scenario (as described in part 3 of our Dust Hazard Analysis series).
The team then assumes that an ignition occurs in each scenario and assesses and describes the potential unmitigated safety and environmental (and sometimes commercial and reputational) consequences. Guidance from a qualified facilitator is crucial at this step.
The team then assesses the likelihood of occurrence of the credible ignition sources. Guidance from a qualified Dust Hazard Analysis facilitator is also crucial at this step.
Risk ranking results and acceptance criteria vary from company to company, but typically the team then uses the consequence and likelihood to develop an unmitigated risk rank for each scenario.
The team then assesses existing preventive and mitigating safeguards for each scenario, using those factors to determine the existing mitigated risk rank for each.
When the mitigated risk ranking does not meet the risk criteria set by the company, then the team typically develops recommendations for additional engineering and/or administrative safeguards. The team may also need to issue recommendations to ensure that safeguards have sufficient specificity, independence, dependability, and auditability, similar to Layer of Protection Analysis (LOPA) independent protection layers, if that is a company expectation.
Finally, the facility follows up on the Dust Hazard Analysis (DHA) recommendations.
If this process sounds a great deal like a HAZOP study to you, then you are right on target. It is also a common practice for companies to adapt their LOPA methods to be suitable for Dust Hazard Analyses for the higher consequence scenarios. It is generally a feasible task to adapt or develop HAZOP and LOPA software templates to be suitable for DHAs. It can even be done in spreadsheets or word processing documents in case of need, though this type of documentation is a little more difficult to initially develop.
An excellent reference for those who wish a deeper dive into DHA methods is Guidelines for Combustible Dust Hazard Analysis, 1st Edition, 2017, by Center for Chemical Process Safety, published by Wiley-AIChE available on-line from your favorite technical bookseller.
The Risk of Dust Hazards
Do you handle potentially combustible dusts at your site? It is difficult to adequately control a hazard that is not well-understood. Even if you have a good-quality PHA, it may not delve deeply enough into the combustible dust topic in accordance with NFPA 652.
NFPA 652 states that existing processes and compartments (e.g., building compartments) shall have a completed DHA by September 7, 2020 (¶ 7.1.1.2) and that the Dust Hazard Analysis shall be reviewed and updated at least every five years (¶ 7.1.4). Are you in compliance? Are you positive your site is managing its combustible dust risks in all phases of operation well enough to prevent a serious explosion?
The Takeaway - Dust Hazard Analysis (DHA)
If you have not previously taken a deep dive into the combustibility properties of your particular dust(s) and completed a Dust Hazard Analysis at your site, now would be a good time to do so. If you do not have the right expertise in your staff to assess dust hazards, consider engaging a process safety consultancy with deep experience and expertise to assist you. Their range of experience enables assessors to share the general and specific methods proven to minimize dust explosion hazards across industry. This independence from the site and company has the best probability of a careful analysis with fresh eyes on the relevant critical systems and leads to more efficient compliance with the necessary standards.
Written by Judith Lesslie, CFSE, CSP
AIChE Webinar: Combustible Dusts and Dust Hazard Analysis: Assess Your Risk
presented by Judith Lesslie - Senior Principal Specialist - aeSolutions
Comments